RepeatPete
Lil-Rokslider
- Joined
- Aug 13, 2023
- Messages
- 104
Time for round 2. Last year I decided to build my own stock and really enjoyed the process. I’m happy with the outcome for a first build, but wanted to try again to tweak some things and build for a different application. The first stock is documented here:
https://rokslide.com/forums/threads/custom-carbon-fiber-stock.322053/
With a good deal on a Kimber from @kad11 and tons of advice and support on all things carbon fiber/stock making from @Gobber I was ready to go again.
This is the starting point: a Kimber Hunter in 6.5 Creedmoor with an 18” barrel. My goal is the perfect eastern US whitetail rifle. I have three main aspects for the stock build.
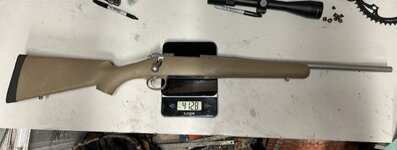
https://rokslide.com/forums/threads/custom-carbon-fiber-stock.322053/
With a good deal on a Kimber from @kad11 and tons of advice and support on all things carbon fiber/stock making from @Gobber I was ready to go again.
This is the starting point: a Kimber Hunter in 6.5 Creedmoor with an 18” barrel. My goal is the perfect eastern US whitetail rifle. I have three main aspects for the stock build.
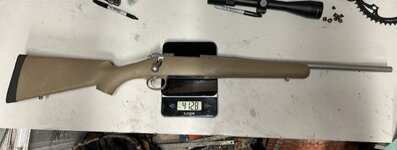
- Shootable design: This means more vertical grip, negatively sloping comb, the top of the recoil pad above the bore line, and a forend that is parallel to the bore. This rifle will rarely, if ever, be shot with a rear bag, so I chose to keep the bottom of the buttstock on a more traditional slope.
- Lightweight: This will be carried pretty much exclusively in my hand, so a lightweight, great balancing rifle is a high priority. The factory Kimber stock, as I bought it with the gel removed, is just at a pound and a half, which is already very lightweight and will be hard to beat. If I end up at that weight or even lighter I’ll be stoked.
- Classic appearance: I appreciate the Rokstok for all its functionality, especially using a rear bag for more long range work, but think it’s pretty ugly. I want to make this stock very functional and easy to shoot, but also want it to look a bit more traditional. I’m envisioning something that looks like a Winchester M70 featherweight, but is lighter and has better ergonomics.