Interesting, I think Kyle or someone got right about 2.4 with the 77s, but can't remember which lower that was. I hope I don't have to do any surgery to make the 79gr drt fit which I have on the way finally. 2.36 works well with the Tennessee arms lower without cutting anything, maybe a little longer would work
I’ll have to go back to my notes. But I think I filed my carbon lower magwell, upper, and barrel extension to allow 2.4” overall. I think I Loaded a couple TMK’s at 2.39”.
My load testing shows a much bigger increase in velocity than I would’ve expected gaining .1” of case capacity.
I’ll see what I can dig up.
For reference, this is from my wife’s Howa mini with a 16” barrel:
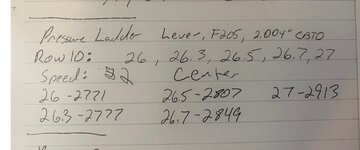
I’ll have to find my notes on OAL at that CBTO, but it was measured with hornady comparator.
Bolt was a little heavy at the 27gr load.
Screamin