Castmaster
Lil-Rokslider
- Joined
- Jul 11, 2023
- Messages
- 198
Ordered a Trijicon Credo HX from Sportsman’s after all the good things I’ve heard about it on this forum but apparently it failed the (Shipping Drop Test). I was pretty excited when it showed up so I immediately opened up the box and held it up to my eye and was pretty surprised to see a bunch of black specs inside the scope… It’s clearly getting returned but thought I’d share my experience.
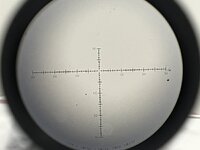
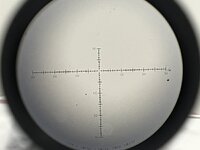