Time for an update on the build process - now its time for making the outer cf shell. Out of experience being well prepared is crucial... Once the resin is mixed and applied it gets really messy really fast. At that stage it sucks to realise you should have made better prep work, cutting breather, peel ply etc.
I try to make all components ready before I start mixing the epoxy. I've cut out peel ply and breather cloth, and made sure its large enough to cover the stock. I also find it helpful to make a few cuts to the peel ply where its wraps at an angle, i.e. around the grip area.
Here the carbon fiber tube is compressed all the way to get max width. Due to the stock being wetted with resin, the tube/sleeve can't slide on like a sock. If/when the cf touches the sticky stock the cf weave starts to disrupt, affecting the integrity/strength (and visually it also ends up looking like a mess) so this should be avoided.
On this build I decided to apply the cf tube in full length of the stock. An alternative is do it in two steps, overlapping in the grip/neck area. The stock was wetted with resin mixed with a few drops of black pigment.
Unlike when cf skinning, I dont want the resin to turn sticky when applying the cf tube. So I pretty much go straight from wetting to putting on the cf tube. I couldn't really take any pictures of this process, as both hands were quite occupied. But I start at the top and try to stretch the cf tube all the way to the bottom with out it touching the stock. When its stretched out passed the buttstock I gently squeeze it to the stock, making sure it adhere to the stock shape.
I stole a few of my daugthers hair ties to help the cf tube to stay in the right spot before I put on a outer layer of resin.
When the stock was fully wetted I cut of the hair ties and wrapped peel ply and breather around the stock.
The last step was putting it all into the vacuum bag and seal it off. When vacuuming I make sure it doesn't wrinkle inside the bag, and if necessary manipulate the wrap/bag. The vaccum pulls out excessive resin through the peel ply and it gets absorbed in the breather. Its clearly doing its job here in the butt and grip area.
The stock was left to cure in vacuum over night.
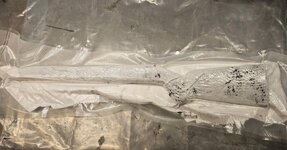