Well, after using it for a season my mind started to work on how I could improve it further. As described in a post above, I began to research better components - stiffer foam core and carbon fiber sleeve (the latter heavily inspired by a youtube clip from the Sako factory, showcasing how they make their carbon fiber stocks).
I got hold of a better/stiffer foam core called Divinycell. In addition to being stiffer, it was also easier to work on. I started out with the normal procedure laminating foam core and carbon fiber:
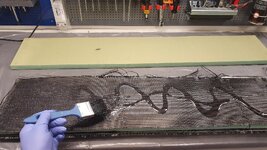
Shaping is primarily done with a sharp knife, wood files and sandpaper.
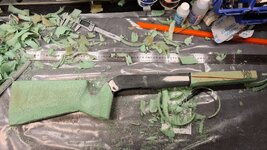
The action is secured with a M6 bolt going thru the grip. I glued in a flush cup as a socket for the bolt head.
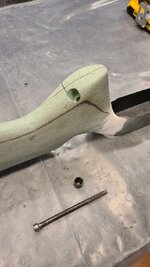
The socket was also secured with a couple of layers for carbon fiber cloth. To make sure the carbon fiber wrapped around the grip area while the resin cured, I used peel ply and thumb tacks.
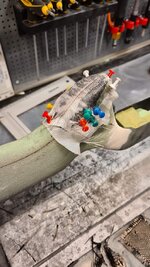
After a couple of layers carbon fiber sleeve and some sanding, the stock looked like this:
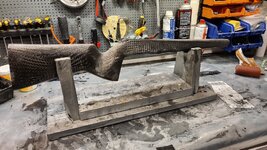
Cutting out the barrel channel:
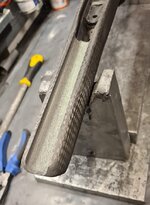
Two layers of the carbon fiber sleeve amounts to an almost 2 mm thick carbon fiber shell:
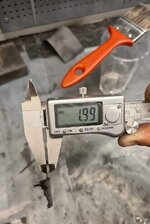
I got hold of a better/stiffer foam core called Divinycell. In addition to being stiffer, it was also easier to work on. I started out with the normal procedure laminating foam core and carbon fiber:
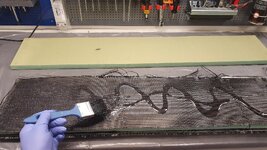
Shaping is primarily done with a sharp knife, wood files and sandpaper.
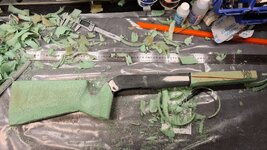
The action is secured with a M6 bolt going thru the grip. I glued in a flush cup as a socket for the bolt head.
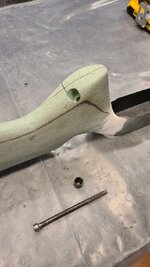
The socket was also secured with a couple of layers for carbon fiber cloth. To make sure the carbon fiber wrapped around the grip area while the resin cured, I used peel ply and thumb tacks.
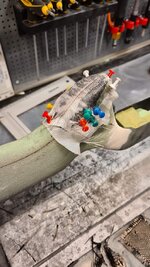
After a couple of layers carbon fiber sleeve and some sanding, the stock looked like this:
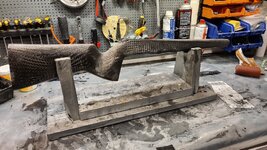
Cutting out the barrel channel:
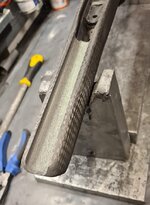
Two layers of the carbon fiber sleeve amounts to an almost 2 mm thick carbon fiber shell:
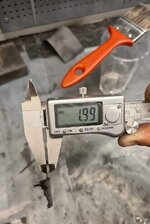