- Thread Starter
- #21
Got it @Marbles thx for the explanation and the drawing! Good idea regardless. I may shim the Alum feet with steel nuts if I need to since the short top rods are already threaded.
So some progress tonight. Mcmaster package showed up, god I love those guys, insanely overpriced but encyclopedic, high quality and as fast as Amazon. The fabrication took about 45min mostly because I’m anal and like things clean and consistent. You could hack it out in less time if you were just getting it done. These parts are going to get beat to piss and possibly melt into a pile so not real sure why I took the effort but old habits die hard. The weight is almost no different at all. I ended up upping the thickness on the tubing a lot for a little more heat sink and that brought it up, but the system is GREAT! Super clean and easy to assemble and nothing to loose anymore. Even if I end up replacing the front threaded rods with steel it’ll be worth it for simplicity. Here’s a quick photo journal:
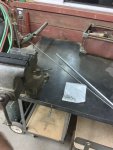
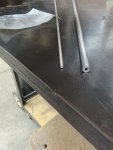
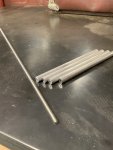
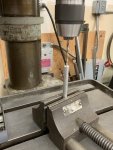
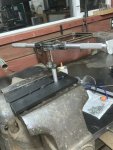
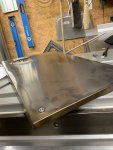
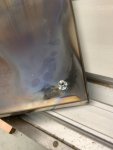
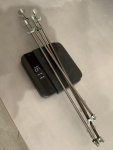
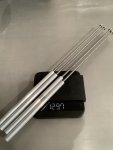
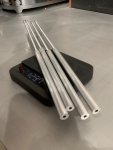
So some progress tonight. Mcmaster package showed up, god I love those guys, insanely overpriced but encyclopedic, high quality and as fast as Amazon. The fabrication took about 45min mostly because I’m anal and like things clean and consistent. You could hack it out in less time if you were just getting it done. These parts are going to get beat to piss and possibly melt into a pile so not real sure why I took the effort but old habits die hard. The weight is almost no different at all. I ended up upping the thickness on the tubing a lot for a little more heat sink and that brought it up, but the system is GREAT! Super clean and easy to assemble and nothing to loose anymore. Even if I end up replacing the front threaded rods with steel it’ll be worth it for simplicity. Here’s a quick photo journal:
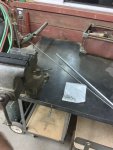
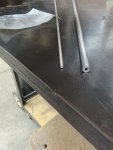
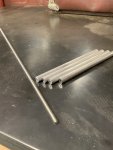
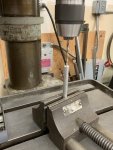
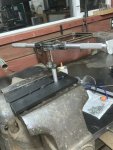
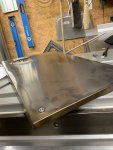
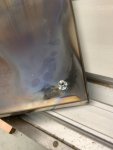
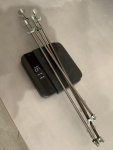
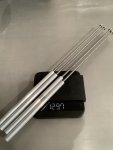
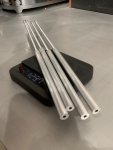
Last edited: