Tumbleweed
Lil-Rokslider
Hey all!
I was given the opportunity to do a review on some of the new 30 Nosler brass released by Bertram. Ryan Avery was kind enough to send me 100ct for testing. First, I'll say that I have no bias for or against Bertram. This is the first time I've used their product. I'm currently running Nosler brass in my custom 30 Nosler. My rifle is a trued Remington 721 with a 27" Broughton 5c 9 twist. It is chambered with Jeff Brozovich's reamer set up for the 215 Bergers.
Initial appearance and packaging:
Brass arrived in a heavy duty zip loc bag. Packaging was adequate.
After pulling a few pieces of brass out I noticed that the necks were dinged. Not uncommon for bulk packaging, it's similar to what I've seen in the past with R-P brass right out of the bag. You will want to at least run a mandrel through the necks before trying to load. The case bodies and shoulders all seemed to be fine.
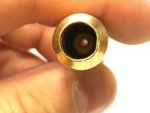
I visually inspected the primer pockets and I could see that many of them were slightly out of round. Enough to cause a leak? I don't think so. I took a picture but it's kind of hard to see.
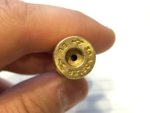
I chose 20 random pieces to do all of my weighing and measuring with. Upon inspection of the flash holes, they appear to be well centered and nicely tapered on the inside. Notice the lines on the inside circumference of the main case body above the flash hole...more on that later.
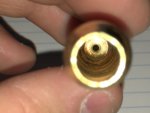
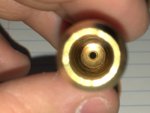
Part of my measurements with these 20 pieces was neck thickness and consistency in thickness. I discovered that there is a raised edge on the outside of the case mouths that cannot be removed with a case debur tool. I had to chuck up the brass in a large drill press and carefully sand the outside edge (only at the end) of the case neck with 400 grit sand paper to be able to get accurate measurements. I ran a mandrel through the case mouth and de-burred the inside.
Now to the numbers: (20 Pieces)
Case Length (20 pieces)
Average: 2.546"
ES: .0015"
SD: .0005"
Case base to shoulder datum (20 pieces)
Average: 2.174"
ES: .008"
SD: .002
Case weight (20 pieces)
Average: 265.36 gr
ES: 5.3 gr
SD: 1.53 gr
Case weight (All 100 rounds...because I wanted to know)
Average: 265.04 gr
ES: 7.5 gr
SD: 1.65 gr
Neck thickness (20 pieces)
Average: .0148"
Average thickness variation: .0021"
Most difference out of 20: .0042"
Least difference out of 20: .001"
Primer pockets
All primer pockets measured exactly .2075"
* I decided not to bother with volume weight testing as there was so much difference in shoulder length. It seemed to me that would not provide useful information until after these cases are fire-formed.
Live fire pressure testing:
H1000, Fed 215GM and 210VLD's seated for .030" jump.
Cases were minimally sized each time to have .002" shoulder bump.
Cases were trimmed after each firing, I noticed fast brass growth. I had to trim .007"-.010" each time.
For the purpose of speed on these tests I did not chronograph rounds.
Round 1:
79 grains
Zero pressure signs and easy extraction
No growth in primer pocket
No growth in rim
Web grew .0004"
Round 2:
81 grains
Zero pressure signs and easy extraction
Primer pocket grew .0005" (Now a tight .208")
No rim growth
Web grew .0001" (total .0005")
Round 3:
82 grains
Zero pressure signs on case head, getting some resistance to bolt lift but not excessive. Decided this was max
Primer pocket still .208" but pin gauge fits easily
Rim grew .0002"
No web growth
Round 4:
82 grains
Still zero pressure signs on case head, getting some resistance to bolt lift but not excessive.
Primer pocket grew another .0005" (Now .2085")
Rim grew another .0005" (Total .0007")
No web growth
Totals
Primer pocket: .001" growth
Rim: .0007" growth
Web: .001" growth
This is where I stopped the test when I realized I had a visible crack starting on the entire circumference of the case 1/4" above the start of the extractor cut taper.
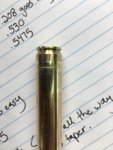
So obviously this was a show stopper. I used my dremel to cut apart the case to investigate.
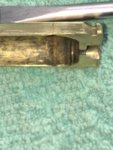
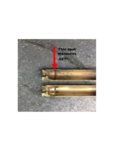
Looks to me like a serious issue with a forming mandrel of some type. As you can see in the photos there's a thin area created in the forming process that produced a really weak spot.
For reference, here's a pic of a piece of R-P RUM brass (top) that has been fired 12 times with top end loads.
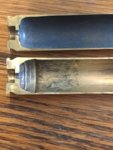
So curiosity got the best of me, I wanted to know if this was a fluke or if there were more cases like this. I cut apart another random piece out of the 100. As you can see, this case had no issues.
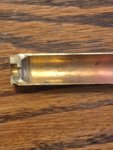
I shined a flashlight into about 15 more cases but couldn't visually see similar issues. However, it's hard to tell what you're seeing looking in at that angle. I don't have a bore scope so there's really no way for me to truly know from the outside if a particular case will have an issue like the failed case. I guess you could slide a pick tool down inside and check each case. I think the point is, we shouldn't have to do that on brand new, expensive cases.
As mentioned above, if you look at the photos of the flash holes you can see pretty aggressive tooling marks down towards the bottom of the case wall. I suspect if this case was fired 3-5 times there would be cracking issues.
Final thoughts:
Would I consider using this brass for my personal rifle? No, here's why:
1. The unknown issue with case web cracking and internal case damage
2. Price. $235 for 100ct. Granted I didn't have to buy these, but I can't see myself paying that much for 100 pieces of brass even IF they were perfect.
3. Case neck thickness variation...I would need to neck turn
4. Case weight variation...I would need to sort cases (volume weights may show more consistency?)
5. Brass seems to grow at an excessive rate even when only bumping shoulder .002". I needed to trim .007"-.010" after every firing. 82 grains was not an excessively hot load in my rifle.
Thank you Ryan Avery for the opportunity to test these cases! I hope this has provided useful information for anyone considering an alternative to the Nosler brand cases.
Jesse
I was given the opportunity to do a review on some of the new 30 Nosler brass released by Bertram. Ryan Avery was kind enough to send me 100ct for testing. First, I'll say that I have no bias for or against Bertram. This is the first time I've used their product. I'm currently running Nosler brass in my custom 30 Nosler. My rifle is a trued Remington 721 with a 27" Broughton 5c 9 twist. It is chambered with Jeff Brozovich's reamer set up for the 215 Bergers.
Initial appearance and packaging:
Brass arrived in a heavy duty zip loc bag. Packaging was adequate.
After pulling a few pieces of brass out I noticed that the necks were dinged. Not uncommon for bulk packaging, it's similar to what I've seen in the past with R-P brass right out of the bag. You will want to at least run a mandrel through the necks before trying to load. The case bodies and shoulders all seemed to be fine.
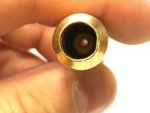
I visually inspected the primer pockets and I could see that many of them were slightly out of round. Enough to cause a leak? I don't think so. I took a picture but it's kind of hard to see.
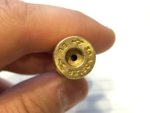
I chose 20 random pieces to do all of my weighing and measuring with. Upon inspection of the flash holes, they appear to be well centered and nicely tapered on the inside. Notice the lines on the inside circumference of the main case body above the flash hole...more on that later.
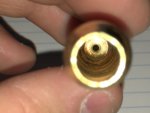
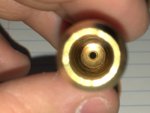
Part of my measurements with these 20 pieces was neck thickness and consistency in thickness. I discovered that there is a raised edge on the outside of the case mouths that cannot be removed with a case debur tool. I had to chuck up the brass in a large drill press and carefully sand the outside edge (only at the end) of the case neck with 400 grit sand paper to be able to get accurate measurements. I ran a mandrel through the case mouth and de-burred the inside.
Now to the numbers: (20 Pieces)
Case Length (20 pieces)
Average: 2.546"
ES: .0015"
SD: .0005"
Case base to shoulder datum (20 pieces)
Average: 2.174"
ES: .008"
SD: .002
Case weight (20 pieces)
Average: 265.36 gr
ES: 5.3 gr
SD: 1.53 gr
Case weight (All 100 rounds...because I wanted to know)
Average: 265.04 gr
ES: 7.5 gr
SD: 1.65 gr
Neck thickness (20 pieces)
Average: .0148"
Average thickness variation: .0021"
Most difference out of 20: .0042"
Least difference out of 20: .001"
Primer pockets
All primer pockets measured exactly .2075"
* I decided not to bother with volume weight testing as there was so much difference in shoulder length. It seemed to me that would not provide useful information until after these cases are fire-formed.
Live fire pressure testing:
H1000, Fed 215GM and 210VLD's seated for .030" jump.
Cases were minimally sized each time to have .002" shoulder bump.
Cases were trimmed after each firing, I noticed fast brass growth. I had to trim .007"-.010" each time.
For the purpose of speed on these tests I did not chronograph rounds.
Round 1:
79 grains
Zero pressure signs and easy extraction
No growth in primer pocket
No growth in rim
Web grew .0004"
Round 2:
81 grains
Zero pressure signs and easy extraction
Primer pocket grew .0005" (Now a tight .208")
No rim growth
Web grew .0001" (total .0005")
Round 3:
82 grains
Zero pressure signs on case head, getting some resistance to bolt lift but not excessive. Decided this was max
Primer pocket still .208" but pin gauge fits easily
Rim grew .0002"
No web growth
Round 4:
82 grains
Still zero pressure signs on case head, getting some resistance to bolt lift but not excessive.
Primer pocket grew another .0005" (Now .2085")
Rim grew another .0005" (Total .0007")
No web growth
Totals
Primer pocket: .001" growth
Rim: .0007" growth
Web: .001" growth
This is where I stopped the test when I realized I had a visible crack starting on the entire circumference of the case 1/4" above the start of the extractor cut taper.
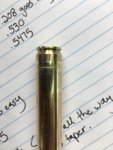
So obviously this was a show stopper. I used my dremel to cut apart the case to investigate.
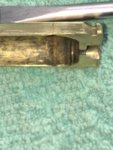
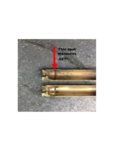
Looks to me like a serious issue with a forming mandrel of some type. As you can see in the photos there's a thin area created in the forming process that produced a really weak spot.
For reference, here's a pic of a piece of R-P RUM brass (top) that has been fired 12 times with top end loads.
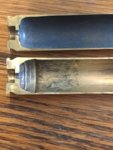
So curiosity got the best of me, I wanted to know if this was a fluke or if there were more cases like this. I cut apart another random piece out of the 100. As you can see, this case had no issues.
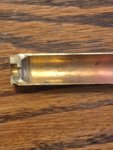
I shined a flashlight into about 15 more cases but couldn't visually see similar issues. However, it's hard to tell what you're seeing looking in at that angle. I don't have a bore scope so there's really no way for me to truly know from the outside if a particular case will have an issue like the failed case. I guess you could slide a pick tool down inside and check each case. I think the point is, we shouldn't have to do that on brand new, expensive cases.
As mentioned above, if you look at the photos of the flash holes you can see pretty aggressive tooling marks down towards the bottom of the case wall. I suspect if this case was fired 3-5 times there would be cracking issues.
Final thoughts:
Would I consider using this brass for my personal rifle? No, here's why:
1. The unknown issue with case web cracking and internal case damage
2. Price. $235 for 100ct. Granted I didn't have to buy these, but I can't see myself paying that much for 100 pieces of brass even IF they were perfect.
3. Case neck thickness variation...I would need to neck turn
4. Case weight variation...I would need to sort cases (volume weights may show more consistency?)
5. Brass seems to grow at an excessive rate even when only bumping shoulder .002". I needed to trim .007"-.010" after every firing. 82 grains was not an excessively hot load in my rifle.
Thank you Ryan Avery for the opportunity to test these cases! I hope this has provided useful information for anyone considering an alternative to the Nosler brand cases.
Jesse