TaperPin
WKR
- Joined
- Jul 12, 2023
- Messages
- 5,350
35 Whelen explained it well. I’d just add, it helps to get a meaningful measurement if the micrometer touches the brass in the exact same place. A sharpie mark can be made, or simply lining up on a letter in the head stamp works just as well. When you’re learning the technique it’s fun to load up 6 or so cases with loads from max on down. I number the cases with the load and a sharpie #1 through #6 and write down the case head diameter. Each time the same case is loaded with the same load and expansion is recorded. It will quickly become clear which loads are not causing much expansion and which are - if you continue with enough shots the cases begin to develop separation rings or loose primer pockets, you now know for that brass how much expansion correlates to case life for other loads. It’s fun watching the progression. At one time this technique was included in some reloading manuals, but it must have caused more confusion than it was worth. Careful measuring can’t be stressed enough or the numbers will seem quite random. A .0001” micrometer is also essential - even the $30 Shars brand will take reliable measurements, and used NSK brand can often be found for about the same price and are top quality. Poland micrometers are also affordable used and I’ve seen them for $20 in good condition. All the kids in our family and extended family get one as gifts - most don’t measure case head expansion, but at least they have the tool and know how to go about it.So if you measure case head expansion with a micrometer what change in dimension are you looking for? Alternatively do you just take a piece of brass and shoot it 8 times and if it survives you're good?
Yep, pressures judged by the number of times a case can be reloaded works well to avoid over pressures and is as easy as firing the same case a number of times, but that is hard to do if the range is hard to get to. Feeling inside the case with a paper clip for case head thinning isn’t required, but is really interesting to feel the thinning start and gradually progress - you can feel the thinning section a number of reloads before it shows a ring on the outside and that ring shows up one or two reloads before the case will actually split. Most people are surprised it’s so easy to feel a minor ring many shots before the case is toast.

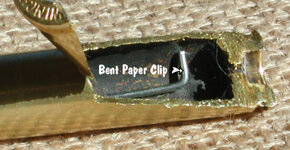
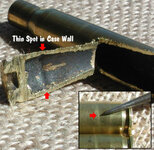