doncarpenter
WKR
So, the pack build-a-long thread motivated me and got me thinking. I have a 26" tactical duplex, for a short time I had a 22" tactical duplex with 22 mag and really liked the shorter frame but couldn't justify having two duplexes. I figured I could make a shorter duplex and use the shoulder straps, hipbelt, and lumbar pad from the other frame.
I have zero experience sewing but I have always been the kind of person who isn't afraid of working with my hands and learning from my mistakes. My sewing machine is a 1930 singer model 66. Its a good old workhorse that does a straight stitch only. It isn't beefy enough to go through the hdpe but it will go through quite a bit of nylon layers.
I decided to go with a 23" frame, I have a 21" torso and it would be a perfect height for busting brush and not get in the way, and still have shoulder lift.
Materials:
500d cordura
2 inch nylon webbing
1 inch nylon webbing
.063" hdpe frame sheet
Aluminum stays
#69 bonded nylon thread
3mm coyote spacer mesh
1 inch open cell foam
1 inch grosgrain binding tape
1 inch and 2 inch hook and loop
1 inch looplocs
1 inch ladderlocks
7/16" grommets
*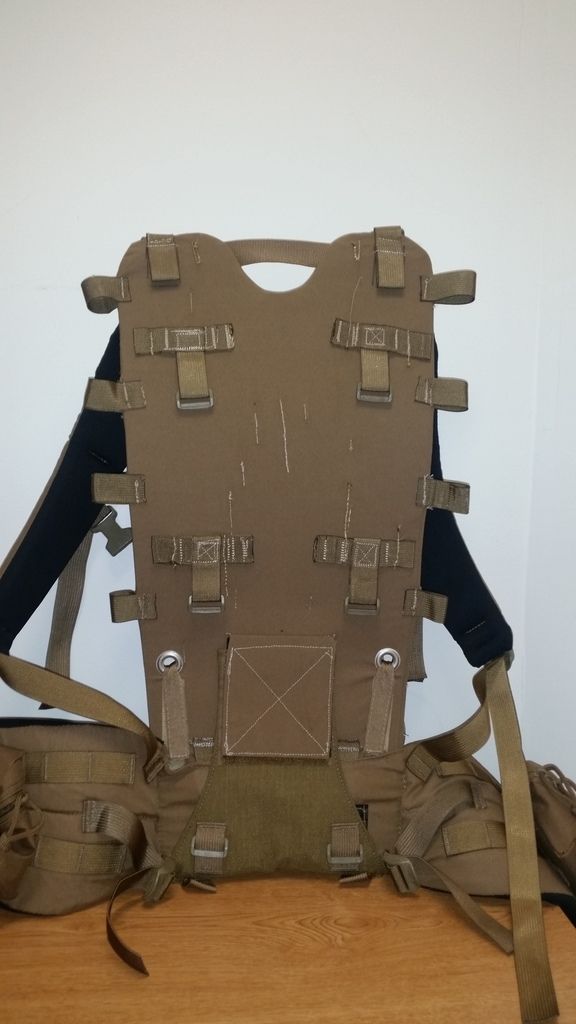
Please ignore the stitching, I apparently can't sew a straight line to save my life.
*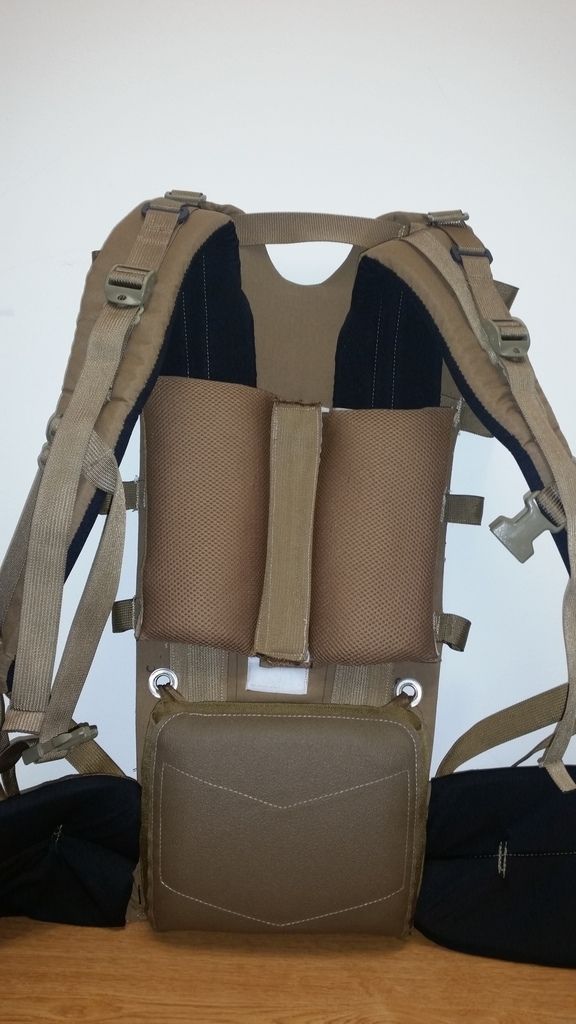
The project turned out functional and not pretty, kinda like me. I learned a ton and I also learned how much I don't know, which is a lot. I like sewing, and I am already planning my next project.
To finish the project and make it structurally more substanstial I picked up a speedy stitcher sewing awl to punch through the hdpe. I noticed that when the curved stays were added and the frame took shape the concave side of the frame the cordura started pulling away. It worked fantastic and I wish I had it a while ago, its great for repairs too. I am gonna pick up a smaller needle for it so I can use the #69 bonded nylon thread with it because the large needle punches a whopper of a hole through.
Sent from my SAMSUNG-SM-G900A using Tapatalk
I have zero experience sewing but I have always been the kind of person who isn't afraid of working with my hands and learning from my mistakes. My sewing machine is a 1930 singer model 66. Its a good old workhorse that does a straight stitch only. It isn't beefy enough to go through the hdpe but it will go through quite a bit of nylon layers.
I decided to go with a 23" frame, I have a 21" torso and it would be a perfect height for busting brush and not get in the way, and still have shoulder lift.
Materials:
500d cordura
2 inch nylon webbing
1 inch nylon webbing
.063" hdpe frame sheet
Aluminum stays
#69 bonded nylon thread
3mm coyote spacer mesh
1 inch open cell foam
1 inch grosgrain binding tape
1 inch and 2 inch hook and loop
1 inch looplocs
1 inch ladderlocks
7/16" grommets
*
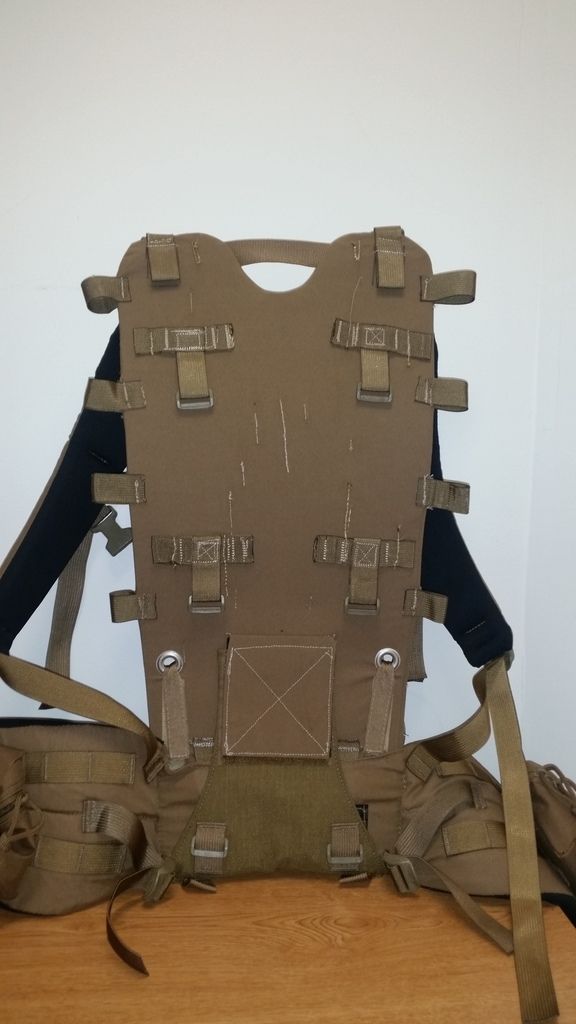
Please ignore the stitching, I apparently can't sew a straight line to save my life.
*
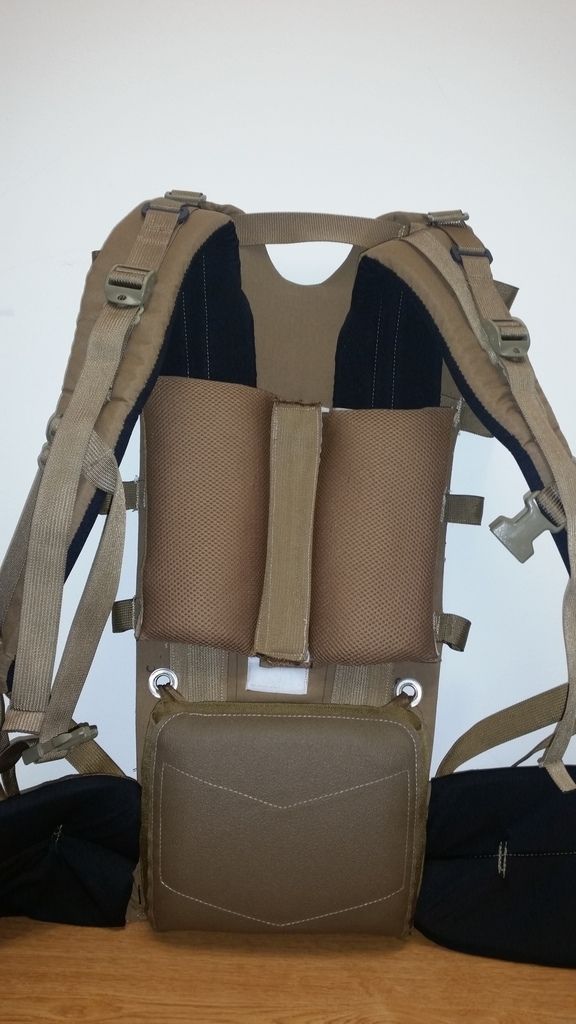
The project turned out functional and not pretty, kinda like me. I learned a ton and I also learned how much I don't know, which is a lot. I like sewing, and I am already planning my next project.
To finish the project and make it structurally more substanstial I picked up a speedy stitcher sewing awl to punch through the hdpe. I noticed that when the curved stays were added and the frame took shape the concave side of the frame the cordura started pulling away. It worked fantastic and I wish I had it a while ago, its great for repairs too. I am gonna pick up a smaller needle for it so I can use the #69 bonded nylon thread with it because the large needle punches a whopper of a hole through.
Sent from my SAMSUNG-SM-G900A using Tapatalk