Magnum61
Lil-Rokslider
I had a crazy day at the range today. I did 3 Satterly tests with my 300 win mag (first time to test the method)
At first, I thought my chronograph was broken because I've never seen anything past 3110fps with a 180 in my 300 win mag. Luckily there was a great guy at the range with a radar that came over and helped to see if my chrono was broken. This exact gun at 2 other loads [210 Berger @ 2865fps] & [200 Accubond @ 2920fps]. I wanted to share this to make sure Something isn't going wrong. I marked in the data where the bolt went sticky from pressure.
Let me know if you're seeing anything I'm not. I've never seen 180's out of a 300win mad at these velocities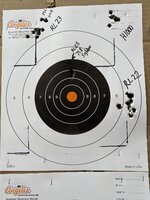
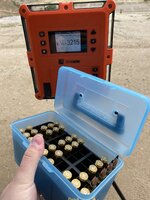
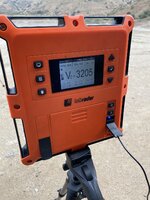
Gun:Rem700 Build
26" Lilja 3 Groove 1/11"
300 win mag
DATA:
180 Swift Scirocco
OAL-Ogive:
3.798 (.050 jump)
H1000 - 81g Max Load (Nosler Manual)
81
80.8
80.6
80.4
80.2 - 3253 (Stiff & Primer flow) Stopped
80 - 3244 (light stiff)
79.8 - 3244 (light stuff)
79.6 - 3252 (sticky)
79.4 - 3244
79.2 - 3244
79 - 3197
RL23 - 73.5 Max load (Nosler Manual)
73.6 - 3182
73.4 - 3182
[Stacked on target (above)]
73.2 - 3167
73 - 3189 (Sticky)
72.8 - 3167
72.6 - 3159
72.4 - 3144
72.2 - 3152
72 - 3152
71.8 - 3108,3115, 3114
——————
RL22
76.6 - 3205
76.4 - 3205
76.2 - 3197
76 - 3189 (3205 radar confirmed)
75.8 - 3159
75.6 - 3159
75.4 - 3144
75.2 - 3144
75 - 3129
74.8 - 3144
At first, I thought my chronograph was broken because I've never seen anything past 3110fps with a 180 in my 300 win mag. Luckily there was a great guy at the range with a radar that came over and helped to see if my chrono was broken. This exact gun at 2 other loads [210 Berger @ 2865fps] & [200 Accubond @ 2920fps]. I wanted to share this to make sure Something isn't going wrong. I marked in the data where the bolt went sticky from pressure.
Let me know if you're seeing anything I'm not. I've never seen 180's out of a 300win mad at these velocities
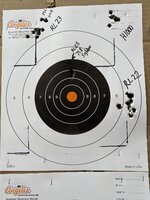
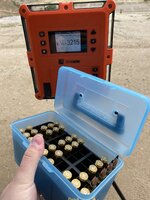
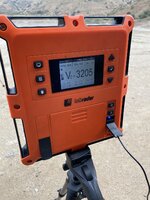
Gun:Rem700 Build
26" Lilja 3 Groove 1/11"
300 win mag
DATA:
180 Swift Scirocco
OAL-Ogive:
3.798 (.050 jump)
H1000 - 81g Max Load (Nosler Manual)
81
80.8
80.6
80.4
80.2 - 3253 (Stiff & Primer flow) Stopped
80 - 3244 (light stiff)
79.8 - 3244 (light stuff)
79.6 - 3252 (sticky)
79.4 - 3244
79.2 - 3244
79 - 3197
RL23 - 73.5 Max load (Nosler Manual)
73.6 - 3182
73.4 - 3182
[Stacked on target (above)]
73.2 - 3167
73 - 3189 (Sticky)
72.8 - 3167
72.6 - 3159
72.4 - 3144
72.2 - 3152
72 - 3152
71.8 - 3108,3115, 3114
——————
RL22
76.6 - 3205
76.4 - 3205
76.2 - 3197
76 - 3189 (3205 radar confirmed)
75.8 - 3159
75.6 - 3159
75.4 - 3144
75.2 - 3144
75 - 3129
74.8 - 3144